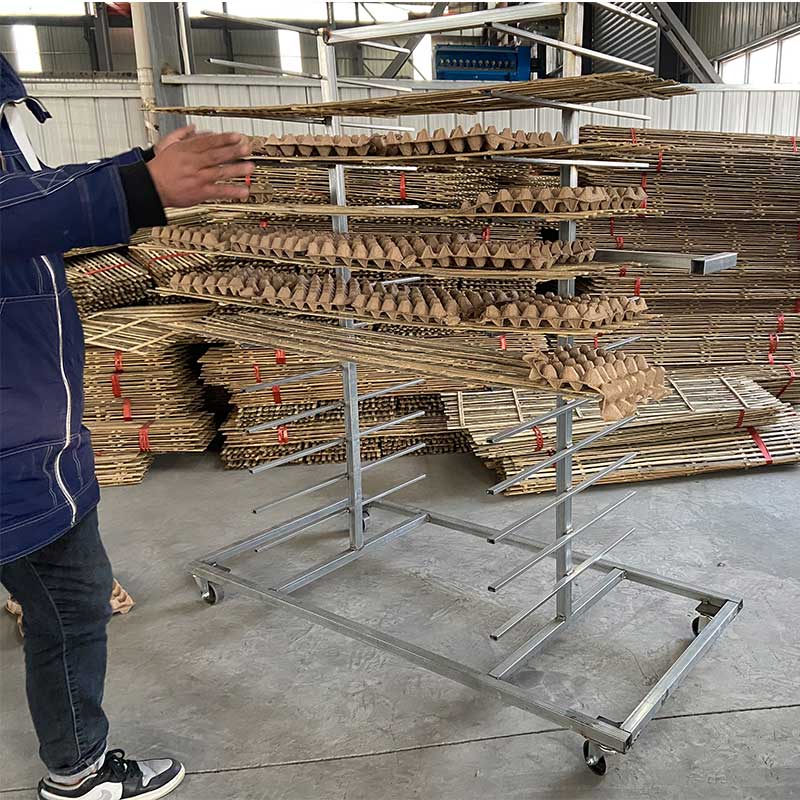
The 3x4 egg tray machine can produce 2,000 pieces of pulp egg trays per hour, which is suitable for small-scale family or workshop-style production. Due to its small output, most customers adopt direct sunlight drying to obtain cost advantages. Manually use a drying rack to transfer the egg tray on the mold, and then use a trolley to push the egg tray to the drying yard for drying. According to the weather conditions, it will generally dry out in about 2 days.
After drying, it is collected manually, packed into plastic bags for moisture-proof treatment, packaged and stored in the warehouse. The raw materials of the paper tray egg tray are waste book paper, waste newspapers, waste paper boxes, all kinds of waste paper and paper scraps from printing plants and packaging plants, paper mill tail pulp waste, etc.The required operators for this egg tray equipment model are 3-5 people: 1 person in the beating area, 1 person in the forming area, and 1-3 people in the drying area.
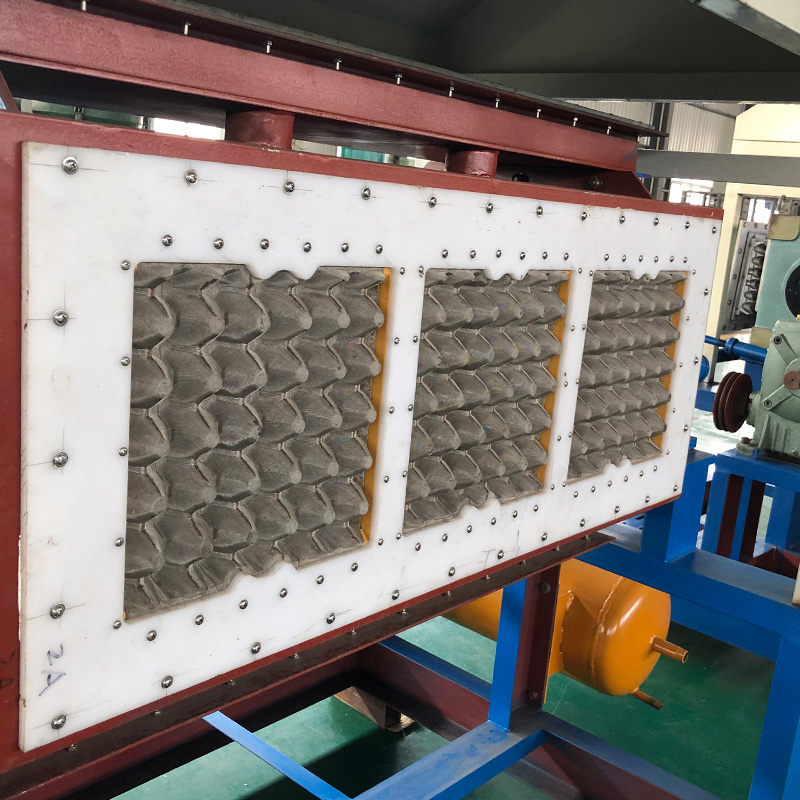
Machine Model | 3*1 | 4*1 | 3*4 | 4*4 | 4*8 | 5*8 |
Yield(p/h) | 1000 | 1500 | 2000 | 2500 | 4000 | 5000 |
Waste Paper(kg/h) | 120 | 160 | 200 | 280 | 320 | 400 |
Water(kg/h) | 300 | 380 | 450 | 560 | 650 | 750 |
Electricity(kw/h) | 32 | 45 | 58 | 78 | 80 | 85 |
Workshop Area | 45 | 80 | 80 | 100 | 100 | 140 |
Drying Area | No need | 216 | 216 | 216 | 216 | 238 |
1. Pulping system
(1) Put the raw materials into the pulping machine, add an appropriate amount of water, and stir for a long time to turn the waste paper into pulp and store it in the pulp storage tank.
(2) Put the pulp in the pulp storage tank into the pulp mixing tank, adjust the pulp concentration in the pulp mixing tank, and further stir the white water in the return tank and the concentrated pulp in the pulp storage tank through the homogenizer.After adjusting into a suitable pulp, it is placed in the pulp supply tank for use in the molding system.
Equipment used: pulping machine, homogenizer, pulping pump, vibrating screen, pulping machine
2. Molding system
(1) The pulp in the pulp supply tank is supplied into the forming machine, and the pulp is adsorbed by the vacuum system. The pulp is passed through the mold on the equipment to leave the pulp on the mold to form, and the white water is adsorbed by the vacuum pump and driven back into the pool.
(2) After the mold is adsorbed, the transfer mold is positively pressed out by the air compressor, and the molded product is blown from the forming mold to the transfer mold, and the transfer mold is sent out.
Equipment used: forming machine, mold, vacuum pump, negative pressure tank, water pump, air compressor, mold cleaning machine
3. Drying system
(1) Natural drying method: Directly rely on the weather and natural wind to dry the product.
(2) Traditional drying: brick tunnel kiln, the heat source can be selected from natural gas, diesel, coal, and dry wood、Heat sources such as liquefied petroleum gas.
(3) Multi-layer drying line: The 6-layer metal drying line can save more than 20% energy than the transmission drying, and the main heat source is natural gas, diesel, liquefied petroleum gas, methanol and other clean energy sources.
-
Waste Paper Recycling Egg Carton Box Egg Tray M...
-
YB-1*3 egg tray making machine 1000pcs/h for bu...
-
1*4 waste Paper Pulp Molding Drying Egg Tray Ma...
-
Automatic paper pulp egg tray production line /...
-
Fully automatic egg tray making machine egg dis...
-
Automatic waste paper pulp egg tray making mach...